
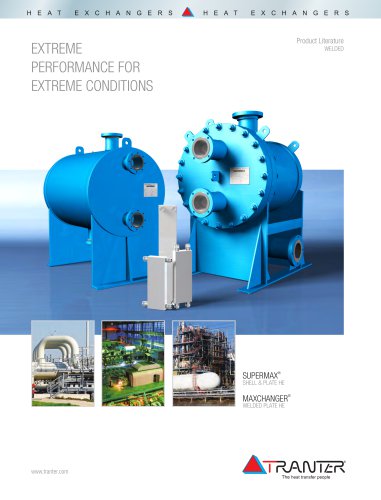
Tranter Spiral Heat Exchangers are utilised for a wide variety of industry applications, especially for process industries. In thermal processing of any kind, PLATECOIL exchangers offer customers more effective thermal control than pipe coil, half-pipe, dimple sheet or gridcoil. Tranter PLATECOIL® prime surface heat exchangers deliver efficient and uniform thermal control in immersion duty jacketing vessels, reactors or dryer shells, within fluidised beds or configured as gas phase heat recovery banks. Prime surface heat exchangers for thermal processes We offer three main types of all-welded heat exchangers: shell and plate, spiral, and prime surface platecoil with connection sizes ranging from 25mm-300mm. All-welded heat exchangers can handle liquids, gases and two-phase mixtures at very high-pressures, as well as at low and high temperatures. They offer high-performance, small sizes and minimal maintenance. They are compact heat exchangers used for extreme temperatures, pressures and specialist designs that exceed gasket limitations. Tranter welded heat exchangers (WHEs) are customised to ensure the highest quality and efficiency.
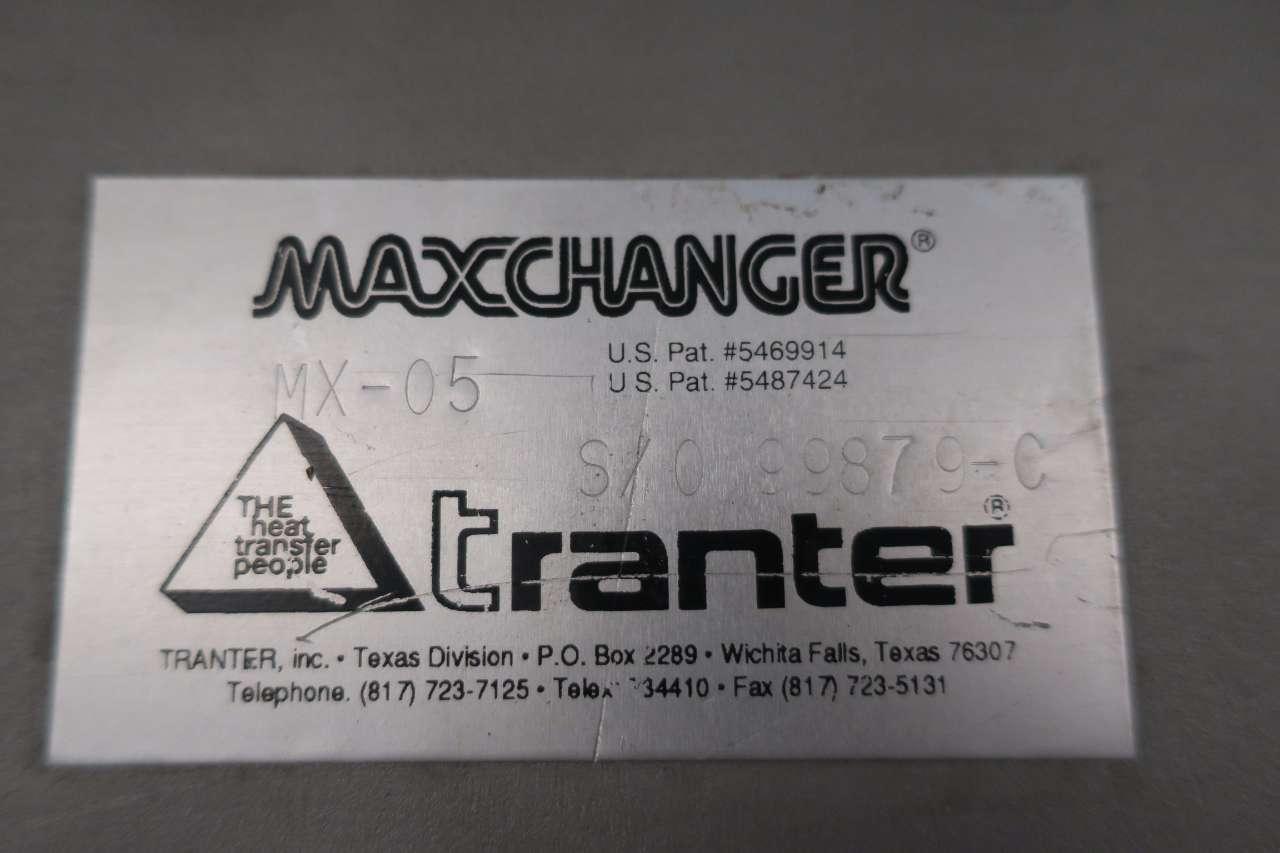
Gaskets are also available in different materials such as NBR, EPDM, VITON and others that suit individual applications.Īll-welded plate heat exchangers for power applications Depending on the applications, heat transfer plates are available in different materials such as SS304, SS316, 254SMO, titanium, Ti-Pd, Hastelloy C-276, nickel, Incoloy and other industrial materials.
#Tranter maxchanger manual#
See the Platecoil® Data Manual for configurations, sizes and materials.With the gasket acting as a sealing media between the heat transfer plates, the PHE can be easily opened for cleaning and maintenance purposes. Type 316L SS PLATECOIL® units are available in 14 and 16 gauge (1.9 mm and 1.5 mm) material. Carbon steel PLATECOIL® are available in 12 and 14 gauge (2.7 mm and 1.9 mm) material. In addition to carbon steel and stainless steel, PLATECOIL® can be fabricated from such materials as Monel, nickel and a variety of other corrosion resistant materials.
#Tranter maxchanger series#
Other 300 series stainless steels are available.
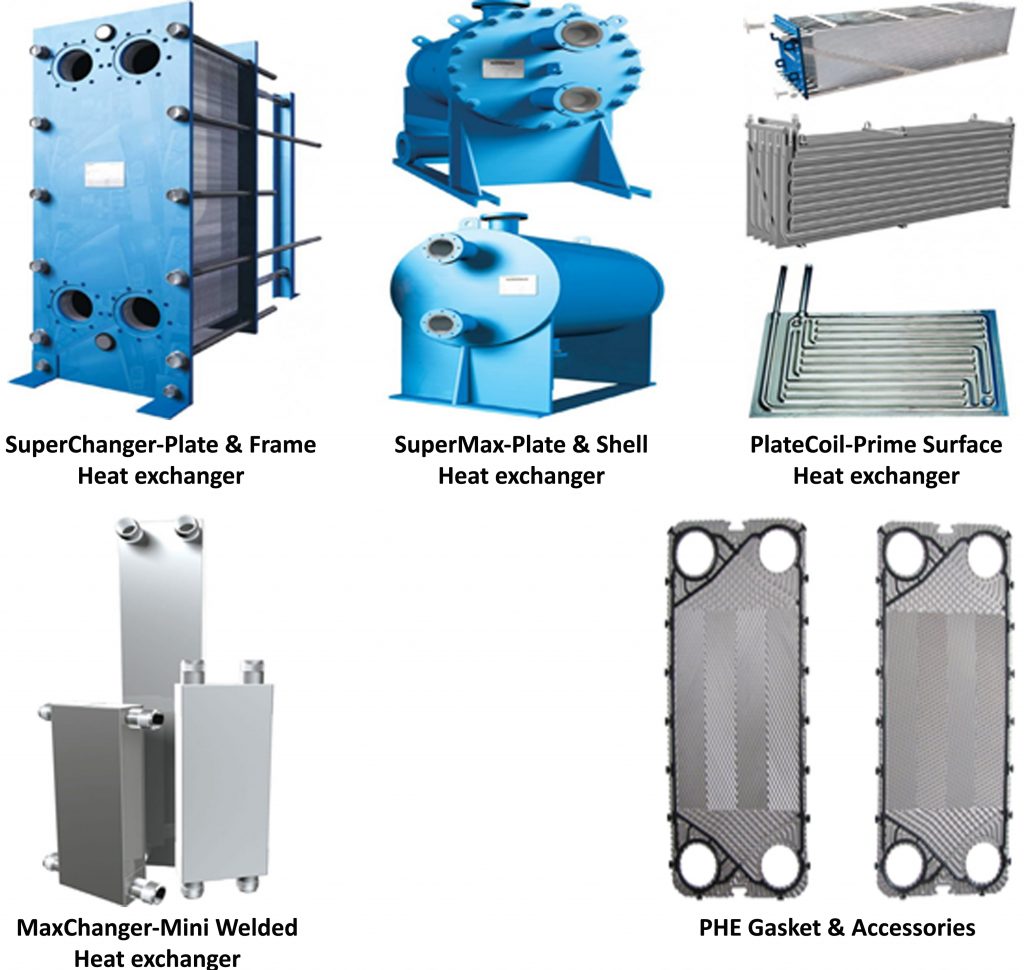
carbon and 0.25 to 0.50% manganese) and Type 316L SS. Materials Standard PLATECOIL® materials include Type SA-414 SS (0.15% max. Large pass, heavy gauge PLATECOIL® is another option available to satisfy requirements for high internal flow rates, low pressure drops and rugged use. Several types of surface finishes can be provided to minimize fouling and reduce maintenance. Construction PLATECOIL® can be bent, rolled, or otherwise formed into virtually any configuration. Orders can often be shipped within a matter of a few days. A large inventory of standard PLATECOIL® is maintained. Each unit is hydrostatically pressure tested before shipping to assure structural integrity. PLATECOIL® is manufactured in compliance with strict quality control standards. Length dimensions range from 584 mm to 3, 632 mm (23 in. Standard PLATECOIL® panels are available in more than 300 sizes widths range from 305 mm to 1, 092 mm (12 in. When welded together, the embossings form a series of well-defined passages through which the heat transfer media flows. PLATECOIL® Prime Surface Heat Exchangers are fabricated from two metal sheets, one or both of which are embossed. Flexibility for a wide variety of applications - High-efficiency plate pattern designs and flow configurations - Unique, neutral-plane gasket groove design and the ability to configure PHE units in a parallel or diagonal flow configuration - Ease if assembly or disassembly for inspection, maintenance and capacity expansion View Complete Details The unit also offers “U” or “K “values 3 to 6 times higher than shell & tube exchangers. Features - Outstanding efficiency in transferring heat from one liquid to another OR from steam to liquid - Compact footprint – using just 20–50% of a shell & tube Heat Exchangers - Offers variety of configurations through Modular exchange system combining frames, plates and connections - Approaches of less than 1☌ (2☏). We have begun manufacturing and designing maintenance-friendly value added solutions with an intension to maximize our customer’s process outputs and also their return on investment in our PHE’s. We have gone beyond simply designing Plate Heat Exchangers that meet the specs highlighted by customers. Our Heat Exchangers have been designed based on the feedback from customers. Tranter is entering its fifth decade of engineering and manufacturing Gasketed Plate Heat Exchangers.
